企业为什么要推行TPM管理?
TPM是一种全员参与的生产维修方式,其主要点就在“生产维修”及“全员参与”上。通过建立一个全系统员工参与的生产维修活动,使设备性能达到最优,降低成本,提高产品质量,最终提高设备总效率的最直接最有效的途径。 华昊企管在多个行业及上千家企业积累了丰富的 TPM 推行经验。能根据不同行业的特点和企业的实际需求,量身定制专属的 TPM 方案。
企业没有推行TPM管理前,是否会存在下列情况:
- 现场脏、乱、差、设备综合利用率低下
- 设备经常故障,严重影响生产的连续性
- 设备无点巡检标准,缺乏系统性管理
- 人员自主保全AM意识匮乏,执行不到位
- 人员专业保全PM管理薄弱,设备部门忙于救火
- 六大指标PQCDSM缺乏有效提升方法
- 缺少系统性的设备维护管理标准
- 现场浪费随处可见,员工改善意识和氛围匮乏
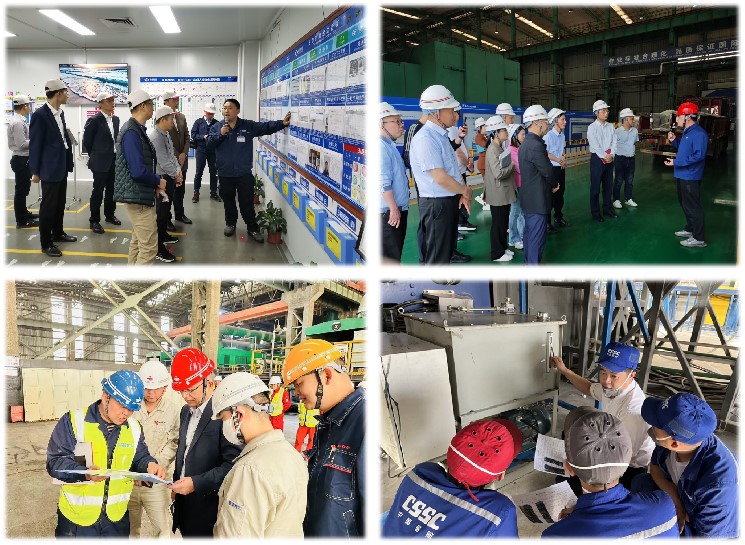
什么是全员设备管理TPM?
1. TPM的概念
TPM(Total Productive Maintenance)中文译名叫全员生产维护,又译为全员生产保全。也可称为“全员设备管理”。这是日本人在70年代提出的,是一种全员参与的生产维修方式,其主要在“生产维修”及“全员参与”上。通过建立一个全系统员工参与的生产维修活动,使设备性能达到最优。
2. TPM全员设备管理的特点
- TPM的特点就是三个“全”,即全效率、全系统和全员参加。
- 全效率:指设备生命周期费用评价和设备综合效率。
- 全系统:指生产维修系统的各个方法都要包括在内。即是PM、MP、CM、 BM等都要包含。
- 全员参加:指设备的计划、使用、维修等所有部门都要参加,尤其注重的是操作者的自主小组活动
3. TPM全员设备管理的八大支柱
企业通过华昊企管实施TPM管理带来的收益
一、设备效率维度:提升综合利用率
- 减少停机损耗:通过预防性维护(如日常点检、定期保养)降低设备故障频率,避免突发停机导致的生产中断。
- 优化性能表现:通过全员参与的维护活动(如自主保养、专业检修),保持设备精度和运行效率,减少速度损失和不良品率。
二、成本控制维度:降低全生命周期成本
- 减少停机损耗:通过预防性维护(如日常点检、定期保养)降低设备故障频率,避免突发停机导致的生产中断。
- 优化性能表现:通过全员参与的维护活动(如自主保养、专业检修),保持设备精度和运行效率,减少速度损失和不良品率。
三、质量保障维度:稳定生产输出
- 控制工艺波动:设备状态的稳定性直接影响产品精度(如加工设备的参数偏差),TPM 通过设备精度校准和故障预防,减少因设备问题导致的质量缺陷。
- 强化过程可控性:通过设备数据记录(如运行参数、维护日志),为质量追溯和工艺优化提供依据。
四、人员管理维度:赋能全员参与
- 培养多能工:员工通过参与设备维护(如自主保养、简单故障排查),提升对设备原理和操作的理解,增强岗位技能。
- 强化责任意识:将设备维护责任下沉到一线,打破 “操作工只用不修、维修工只修不用” 的分工壁垒,形成全员参与的管理文化。
五、安全与合规维度:降低运营风险
- 消除安全隐患:通过设备安全装置检查(如防护栏、急停按钮)和危险源识别,减少机械伤害、电气故障等安全事故。
- 符合环保要求:TPM 涉及设备能耗监测(如耗电、耗材使用)和污染控制(如漏油、废气处理),帮助企业满足环保法规要求
六、管理体系维度:推动精益化升级
- 标准化与系统化:通过建立设备维护标准(如点检表、保养计划)和流程(如故障上报、备件管理),提升管理规范性。
- 数据驱动决策:通过设备运行数据(如 OEE 指标、MTBF/MTTR 分析)量化管理效果,为生产计划和资源调配提供数据支撑。
设备OEE提升
故障时间下降
停机时间下降
设备能耗降低
我们在全员设备管理TPM领域的优势
> 1500 家企业
我们辅导其实施
精益TPM管理
超过十六大行业
管理咨询覆盖范围
完善的管理体系
丰富的方法研究与行业
应用经验
专业、稳定的
顾问团队
保障项目的实施质量