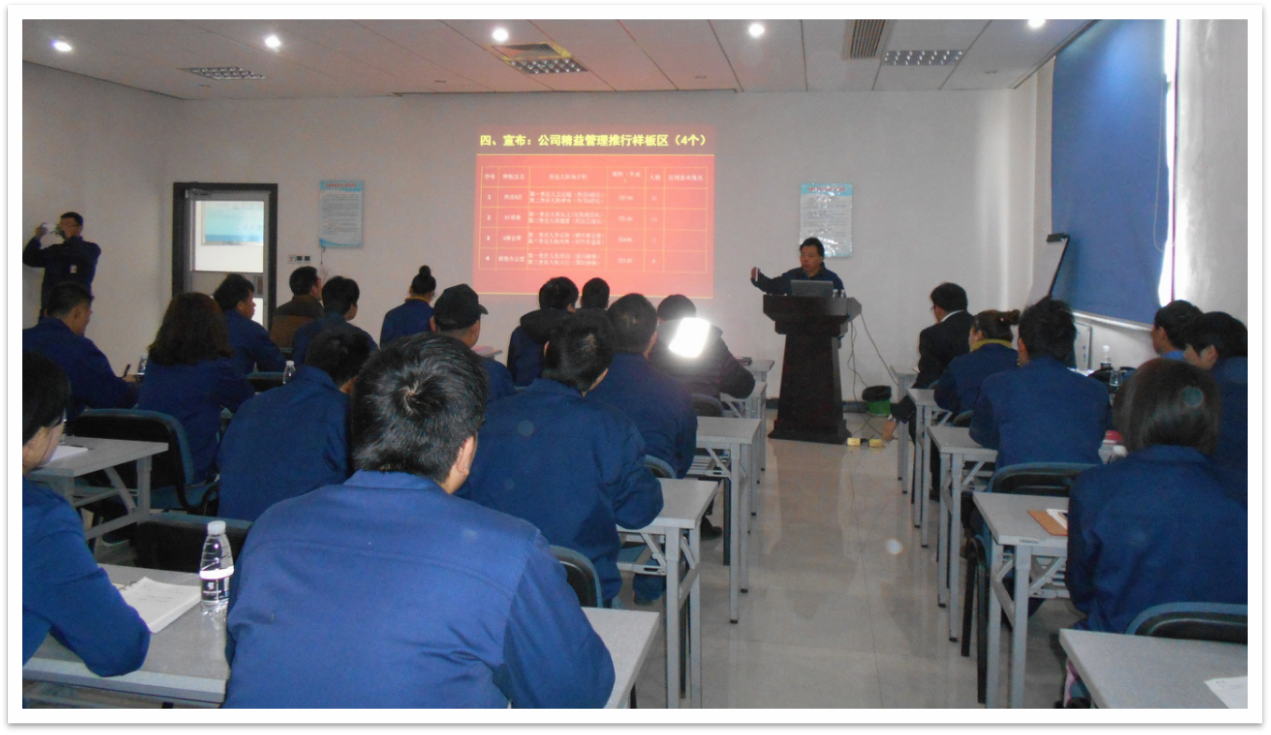
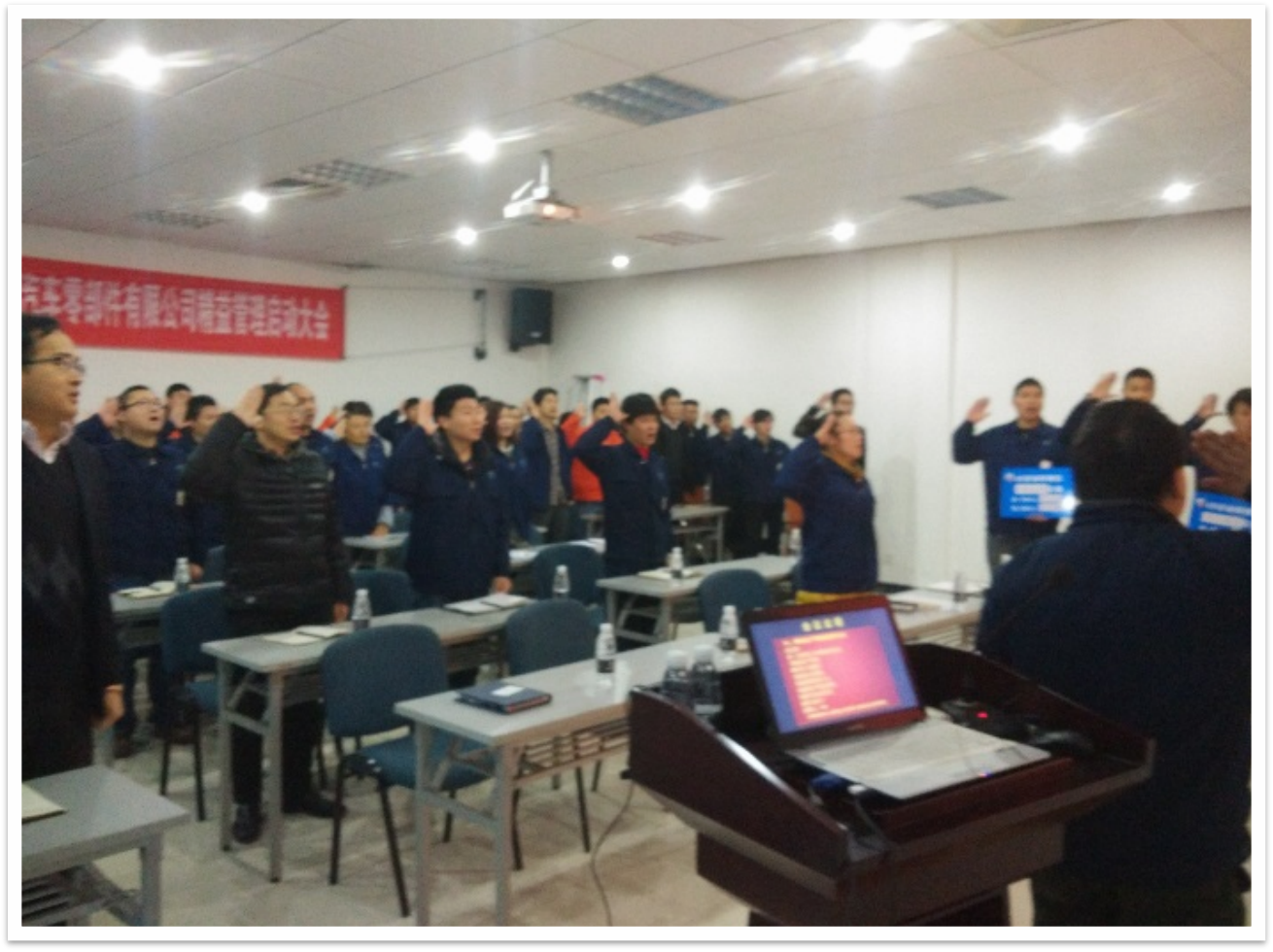
【客户介绍】
浙江万赛成立于2011年,总投资1.5亿元,占地面积46800㎡,建筑面积67000㎡,主要以设计、研发、生产、销售(商用车、乘用车、摩托车及工程机械)制动片及高性能环保摩擦材料为一体的国家高新技术企业,是目前国内最大的盘式刹车片生产基地,是我国刹车片制造行业的领军企业之一。系中国汽车工业协会制动器委员会会员、中国密封摩擦材料协会副会长单位。产品广泛配套于大型客车、传统燃油和新能源汽车、摩托车以及工程机械、轨道交通、飞机等的制动系统,全品类3000多种型号产品,1600多款产品通过E-MARK 认证,通过认证产品的数量在国内同行中占绝对优势。作为一家技术导向型企业,公司始终把品质作为第一要素,坚持精益管理贯穿研发、制造、销售等每个环节,倡导绿色环保,专注产品细节,遵循质量控制的可持续发展路线,通过质量、环境、职业健康与安全三体系认证。
【项目背景】
1、成本与效率压力 原材料、能源、人工成本逐年上升,单纯降价竞争空间不断压缩。 库存积压、停工待料、返工返修等“六大浪费”导致资金占用、交付延期。 2、质量与交付挑战 产品良品率、一次合格率不高,质量事故频发,损害品牌信誉。 供应链协同不足,物料、信息流错配,导致交付周期不可预测。 3、组织与管理瓶颈 部门职能割裂、信息孤岛严重,问题往往被“推诿”或“隔靴搔痒”式解决。 现场管理不到位,一线员工提出的改进建议难以落地,持续改进动力不足。 4、人力资源与文化需求 技能型人才供应短缺,高素质员工希望参与决策、获得成长。 企业亟需建立“以人为本”、人人参与的持续改进文化。
【项目成效】
系统性推进:6S现场管理、设备自主保全、改善提案活动、干部课题活动、班组长培训、KPI指标管理、设备计划保全、设备初期管理、干部课题活动、教育训练、专家级员工培养.....等内容开展,引入精益生产管理理念,通过消除浪费、持续改进,提高生产效率、降低成本、提升质量,最终实现客户满意。公司高层高度重视精益生产的推行,成立了精益生产推进小组,并制定了详细的实施计划,力争通过精益生产项目的实施,将公司打造成为行业内的标杆企业。