一、电子行业管理面临的压力与挑战
电子行业作为技术密集型产业,在快速发展的同时,也面临着诸多管理方面的压力与挑战,具体如下:
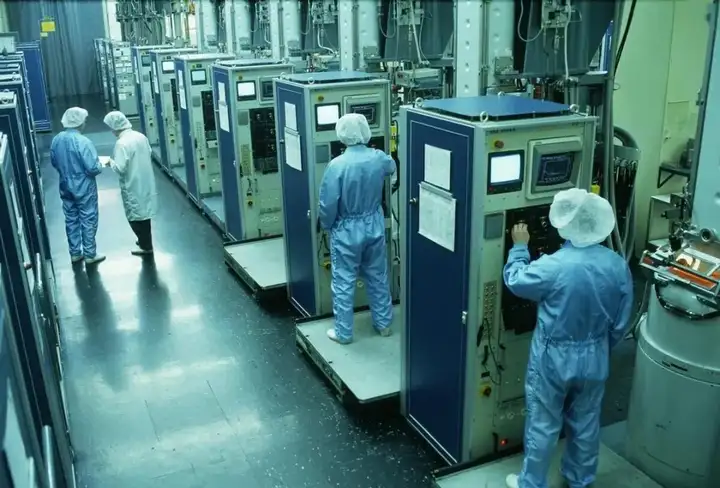
-
技术创新压力:电子行业技术迭代速度极快,新的技术、产品和解决方案不断涌现。企业需要持续投入大量资源进行研发,以跟上行业的技术发展步伐。
例如,在半导体领域,芯片制程工艺不断向更小的纳米级别演进,若企业不能及时掌握先进的制程技术,其产品在性能和功耗上就会落后于竞争对手。
同时,研发新技术需要大量的资金、高端人才和时间成本,且存在研发失败的风险,这对企业的资金实力和风险管理能力都是巨大的考验。 -
市场竞争激烈:电子市场产品种类繁多,消费者需求多样化且变化迅速。一方面,企业要不断推出满足市场需求的新产品,以吸引消费者;另一方面,还要应对来自国内外众多竞争对手的挑战。
例如,智能手机市场竞争激烈,各大品牌不仅要在性能、外观、拍照等方面不断创新,还要在价格上进行竞争,以争夺市场份额。此外,新兴企业凭借创新的商业模式和技术,也在不断冲击传统电子企业的市场地位。 -
供应链管理复杂:电子产品的生产往往涉及众多零部件和原材料,供应链环节众多且复杂。
例如,一台笔记本电脑的生产需要来自全球各地的零部件供应商提供芯片、显示屏、内存、硬盘等关键部件。供应链的任何一个环节出现问题,如原材料短缺、供应商生产中断、运输延误等,都可能影响企业的生产进度和产品交付。
此外,电子零部件的价格波动较大,受市场供需关系、汇率变化等因素影响,企业需要具备良好的供应链风险管理能力,以降低成本和保障供应的稳定性。 -
产品质量与可靠性要求高:电子产品的质量和可靠性直接影响消费者的使用体验和企业的声誉。随着消费者对电子产品品质要求的不断提高,企业需要建立严格的质量控制体系,从原材料采购、生产制造到产品测试和售后,对每一个环节进行严格把控。
例如,汽车电子零部件的质量要求极高,任何一个小的质量问题都可能导致严重的安全事故。同时,电子产品的召回成本巨大,不仅会造成经济损失,还会损害企业的品牌形象。 -
人才短缺与流失:电子行业对高端技术人才和管理人才的需求旺盛,但人才市场的供应相对不足。企业之间对优秀人才的争夺激烈,导致人才流失率较高。
特别是一些掌握核心技术的研发人才和具备丰富经验的管理人才的流失,可能会对企业的研发进度和管理效率产生不利影响。
此外,电子行业技术更新快,员工需要不断学习和提升自己的技能,企业需要投入大量资源进行员工培训,以满足企业发展的需求。 -
法规政策与环保要求:电子行业受到众多法规政策的监管,如产品安全标准、电磁兼容性标准、环保法规等。不同国家和地区的法规政策存在差异,企业需要确保其产品符合各地的法规要求,这增加了企业的合规成本和管理难度。
例如,欧盟的 RoHS 指令限制了电子电气设备中某些有害物质的使用,企业需要对原材料和生产工艺进行调整,以满足环保要求。
同时,随着环保意识的提高,消费者对电子产品的环保性能也提出了更高的要求,企业需要在产品设计和生产过程中考虑环保因素,推动可持续发展。 -
知识产权保护:电子行业技术创新频繁,知识产权保护至关重要。企业的研发成果如专利、商标、软件著作权等,是企业的核心竞争力之一。然而,知识产权侵权行为在电子行业较为常见,企业需要投入大量资源进行知识产权的保护和维权。
同时,不同国家和地区的知识产权法律体系存在差异,企业在国际市场拓展过程中,需要了解并遵守当地的知识产权法规,以避免侵权纠纷和法律风险。
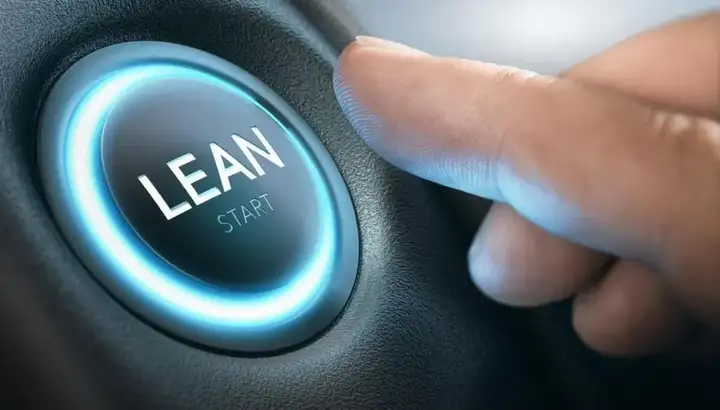
二、电子行业导入精益管理的收益
-
生产效率提升:
电子行业产品更新换代快,生产流程复杂。精益管理通过价值流分析,识别并消除生产过程中的浪费环节,如过度加工、等待时间、不必要的搬运等。
对生产布局进行优化,实现生产线的均衡化生产,减少工序间的瓶颈,提高设备的利用率和员工的工作效率。
例如,在电子产品组装环节,通过合理安排工位和作业顺序,使每个工人的操作更加流畅,减少了物料等待时间,从而提升了整体的组装效率。 -
成本降低:
精益管理注重成本的精细化控制。通过减少库存积压,实施准时化生产(JIT),企业可以降低库存成本,包括仓储成本、资金占用成本等。优化生产流程,降低原材料和能源的消耗,提高生产效率,也能有效降低单位产品的生产成本。
此外,减少次品率和返工率,避免了因质量问题带来的额外成本。 -
产品质量提高:
在电子行业,产品质量至关重要。精益管理强调全员参与质量控制,从原材料采购到产品最终交付的全过程进行严格监控。
通过实施全面质量管理(TQM),运用统计过程控制(SPC)等工具,及时发现和解决质量问题,降低次品率。建立质量追溯体系,能够快速定位质量问题的根源,采取有效的改进措施,提高产品的可靠性和稳定性。 -
响应速度加快:
电子市场需求变化迅速,客户对交货期的要求越来越高。精益管理使企业能够更加灵活地应对市场变化,通过缩短生产周期,提高生产的灵活性和响应速度。
快速换模(SMED)、快速换线等技术的应用,使企业能够在短时间内切换生产不同型号的产品,满足客户的多样化需求。同时,优化供应链管理,加强与供应商的合作,实现信息共享,确保原材料的及时供应,进一步提高了企业的响应能力。 -
员工参与度和士气提升:
精益管理鼓励员工积极参与企业的改进活动,赋予员工更多的自主权和责任感。通过开展持续改善活动(如合理化建议、QC 小组等),员工能够提出自己的想法和建议,为企业的发展贡献力量。
员工的意见得到重视和采纳,会增强他们的归属感和成就感,从而提高工作积极性和士气。此外,精益管理注重员工的培训和发展,为员工提供学习和成长的机会,提升员工的技能水平和综合素质。
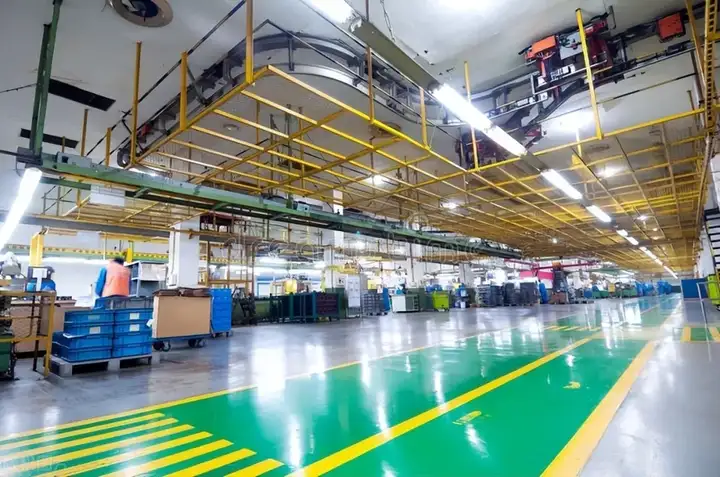
三、精益管理案例说明 —— 丰田旗下电装公司(Denso)
-
公司背景:电装公司是世界著名的汽车零部件生产厂家,在电子部件领域也有广泛的业务。随着市场竞争的加剧,电装公司面临着成本压力、产品质量提升和快速响应客户需求等挑战。为了应对这些挑战,电装公司导入了精益管理理念和方法。
-
精益管理实施举措
-
价值流分析与优化:电装公司对其电子产品的生产流程进行了全面的价值流分析,识别出生产过程中的浪费环节,如过度库存、不必要的搬运和等待时间等。针对这些问题,公司优化了生产布局,将相关工序进行整合,减少了物料的搬运距离和等待时间。同时,实施了看板管理,实现了生产的可视化和准时化,有效降低了库存水平。
-
全员参与的质量控制:电装公司推行全员参与的质量控制理念,从高层管理人员到一线员工都参与到质量改进活动中。公司建立了完善的质量管理制度和流程,运用统计过程控制(SPC)、失效模式与效应分析(FMEA)等工具,对生产过程进行实时监控和分析。通过开展质量培训和教育活动,提高员工的质量意识和技能水平。此外,电装公司还鼓励员工提出质量改进建议,对优秀的建议给予奖励,形成了良好的质量改进氛围。
-
持续改善文化:电装公司建立了持续改善的文化,鼓励员工不断寻找改进的机会。公司设立了专门的改善小组,定期开展改善活动,对生产流程、产品质量、设备维护等方面进行改进。通过实施改善项目,电装公司不仅提高了生产效率和产品质量,还降低了成本,提高了员工的工作满意度和士气。
-
供应商管理:电装公司注重与供应商的合作,建立了紧密的供应链关系。公司对供应商进行严格的评估和管理,选择优质的供应商,并与供应商共享生产计划和需求信息,实现了原材料的准时供应。同时,电装公司还帮助供应商实施精益管理,提高供应商的生产效率和质量水平,共同降低成本,提高整个供应链的竞争力。
实施效果
-
生产效率大幅提升:通过优化生产流程和布局,实施看板管理和准时化生产,电装公司的生产效率提高了 30% 以上,生产周期缩短了 20%。
-
成本显著降低:库存成本降低了 40%,原材料和能源消耗减少了 15%,单位产品生产成本降低了 10%。
-
产品质量显著提高:次品率降低了 50%,产品的可靠性和稳定性得到了大幅提升,客户投诉率降低了 60%。
-
响应速度加快:能够在更短的时间内响应客户的需求,订单交付周期缩短了 30%,提高了客户满意度和市场竞争力。
-
员工士气高涨:员工参与改善活动的积极性大大提高,提出了大量有价值的改进建议,员工的技能水平和综合素质得到了提升,工作满意度和士气显著提高。
电装公司的案例表明,精益管理在电子行业具有巨大的应用潜力和价值。通过导入精益管理,电子企业可以实现生产效率提升、成本降低、质量提高、响应速度加快和员工士气提升等多方面的收益,从而在激烈的市场竞争中取得优势。