制造业通过加工设备实现产品的加工,在人力成本日趋高涨的今天,企业势必会越来越想明白一个道理,如果可以通过自动化设备来代替人工,相信企业主会认真评估实际的ROI,毕竟设备可以7*24H的工作,最主要是没有任何情绪变化。
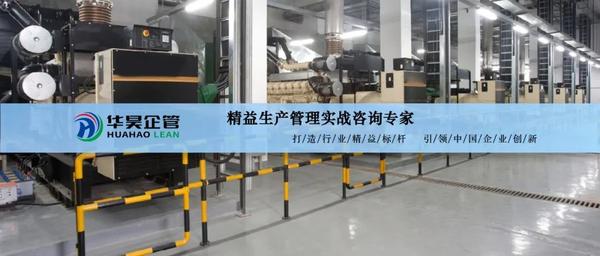
如果从行业的发展方向角度来说,机器设备取代人工是必然的,特别是近期大火的AI ChatGPT,它近乎可以无懈可击的回答大家提出的任何问题,并且问题的答案总是理性而睿智,如果不告诉你是谁在回答问题,可能你会感觉这是一位大贤、或者至少是一位智者,但是总感觉过于理智,这或许就是和人类的根本差异。未来AI的发展难测,是进步或是灾难,可能也只在一部分人的一念之间,大家可以再去回顾一下“黑客帝国”,感受一下可能的未来。
当前AI在工业领域里已经有了部分的应用,主要是在图像及算法上的应用,不应过分神化AI,只有把AI结合到自动化、设备或软件中,借助它的机器学习迭代优势,最终能达到提升质量、提升作业效率或降低成本等实际的目标,AI才真正发挥了其作用。否则它只是一个概念,我们应该知道如果一项技术不能在合理的成本范围内解决某个问题,那么这个技术只能存在于科研或实验室里。AI在工业上的应用潜力,这个话题后续可以再来展开。
那么对于工厂里已经在使用的设备,如何通过系统化流程管理来延长设备使用寿命,减少设备故障率?如何能精确地分析出设备的效率,找到制约因素,提升设备产出能力呢?
01 设备管理主要业务
总结来说,设备管理主要包括两个大方向。
第一个方向是设备的维护保养的管理,这一块的管理核心是通过数字化、流程化的方式将设备的台账、保养计划、保养作业、报修维修及备品备件进行管理。主要目标是通过管理尽可能确保设备不出问题,延长设备的使用寿命。
第二个方向是设备的效率分析,这一块的管理核心是通过综合生产行为及设备实际状况对设备的效率进行详细分析,也就是OEE,即设备综合效率。通常这一块是设备管理比较困难的部分,难点在数据及管理规则,而非系统。设备OEE是可以给企业带来效率改善的实用指标,值得企业花心思去做。
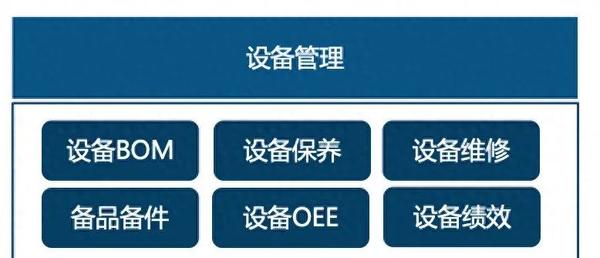
02 设备维保流程
1)设备保养
通常企业设备保养是基于周期性来执行保养的,也有特定的场景是基于加工数量来执行的。周期性的保养执行系统可以自行通过JOB来计算任务时间,实现定期的任务下达及通知。基于加工数量来执行保养的模式,需要通过采集设备的加工数据来执行计算,通常再设定原则冲突原则即可。
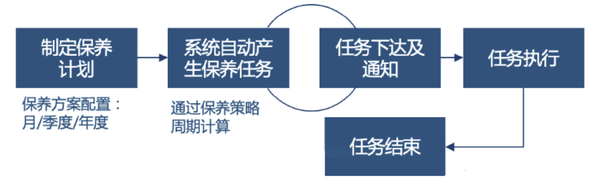
更精细的管理方式是将保养项目与人员分开定义,如机构类保养指定一位设备工程师,电气类保养指定专门的电气工程师,而且不同类型保养项目的保养周期也是不同的。基于这样的模式下,我们在进行保养任务分解时需要考虑基于项目的周期产生任务,同时任务需要权限的分配,规则定义如下:
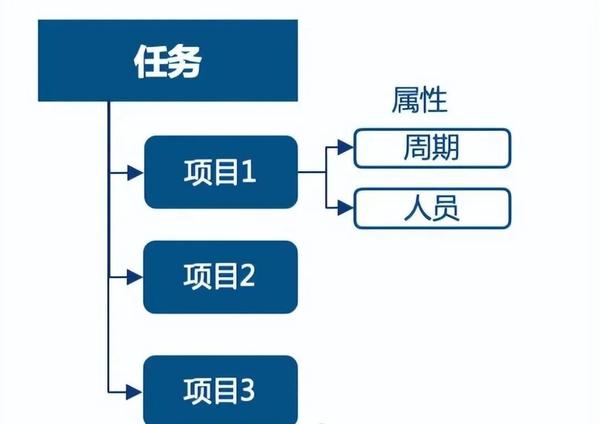
为提升任务的快速通知及作业的便携性,保养任务产生后可以集成企业内部的沟通工具,如钉钉等,进行实时的推送。作业端则通过平板来实现移动化作业,提升作业效率。
2)设备维修管理
生产过程出现设备异常时,由生产人员在系统中发起报修单,填报异常现象。有一项重要的异常分配策略需要定义,主要是根据异常类型及设备区域定义维修组角色。一旦出现报修时通过分配策略把报修单精确的推送给相应的维修组角色,在这个角色组中的设备维修工程师可以接单处理。
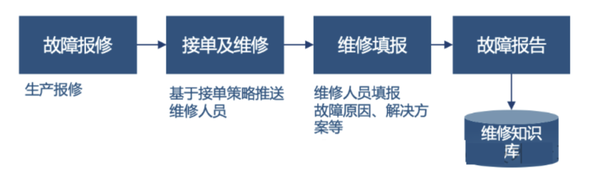
设备报修过程通常流程的发起点也会在Andon中,异常发起后推送异常到相应的角色中,使用Andon的一个优势是在问题得不到及时响应时将触发升级机制,直到问题被处理。
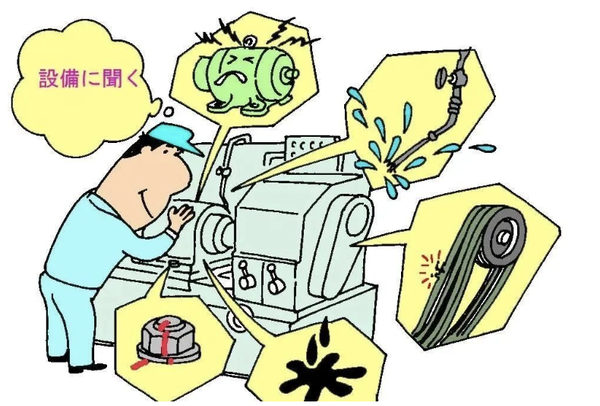
3)设备绩效
设备部门也会关注两个绩效指标来对设备工程师进行评价。
MTTR平均修复时间,用来衡量设备异常后的恢复效率;
MTBF平均故障间隔时间,用来衡量设备的稳定能力;
从实用价值角度看,MTTR适用于企业已经精细化制定各类异常的标准维修工时,在此基础下通过实际的修复时间数据与标准进行比较,可以进行维修能力的评价。但现实情况是工厂里的同一类型设备可能有多个厂商,而且年代也不同,这些干扰将会给这些指标的判断带来无法确定的问题,因此可能MTBF指标很难从实际应用上带来理想的效果。
03 设备OEE
1)标准算法
OEE = Availability × Performance × Quality
Availability即时间稼动率;Performance即性能稼动率;Quality即良品率;计算方法如下表:
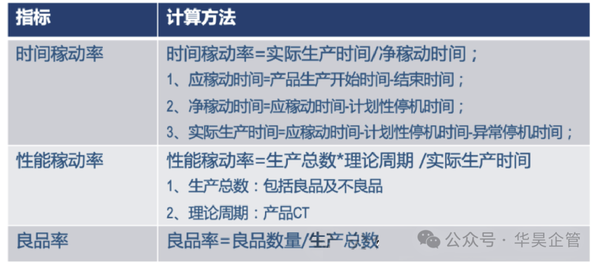
2)统计纬度说明
OEE指标需要考虑统计的最小颗粒度,只有将最小颗粒度层级的各类计算数据获取到,才能进行向上放大的统计,这个是需要设计人员思考清楚的一件事,如果你的客户告诉你说需要查询任一时间点的OEE,基本上你的项目会很难做了,主要问题是客户没有这一块的认知,你需要花费大量的时间来解释。
所以基本上OEE的最小颗粒度是在订单层级,这里要特别说明如果订单的量很大,会跨越多个班次,显然说订单是最小颗粒度是站不住脚的,这样的情况班次就会是最小颗粒度,所以你要考虑清楚这个逻辑细节以及背后的设计思路。
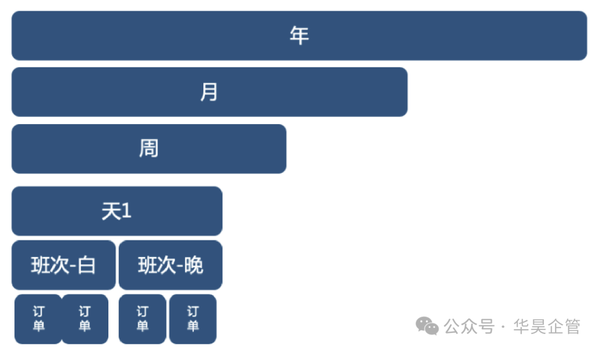
3)数据的获取
数据的获取是OEE计算环节面临最多挑战的地方,借着刚刚的那个场景,如果你发现你的客户是没有任何系统的,那么基本上你的OEE项目可以宣告失败了,没有其它系统支撑OEE是很难计算出来的。
OEE之所以叫设备综合效率是有原因的,因为需要计算它的数据也是非常综合的,我们大概分解一下:
需要计划系统来支撑:计划停机数据等;
需要生产系统来支撑:实际运行时间、异常时间(待料、维修等)、标准工时、加工数量、良品数、废品数量等;
需要数采系统来支撑:设备停机时间、故障时间、空闲时间等;
需要管理来支撑:及时操作系统,及时标记异常,及时上报问题;
4)总结
如果你看到一个企业的OEE数据很低,不要嘲笑;如果很高,不要惊讶,事实和你想的可能是不一样的。
如果你自己在做OEE项目,多花点时间和精力把底层概念理解清楚,多做一些沟通给客户讲清楚,看起来可能多花时间了,其实是更快了。
期望企业主都决定好好的做一做OEE,只是一开始不要把目标定的太高,先评估风险与条件,一步步做,总会有提升。