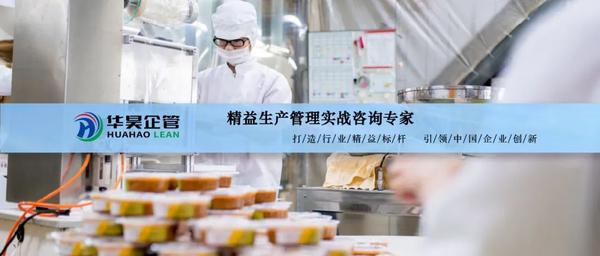
VSM (Value Stream Mapping)价值流程图,源自于丰田的物料和信息流程图,是丰田系统地规划整个供应链的物料和信息流动的核心工具。
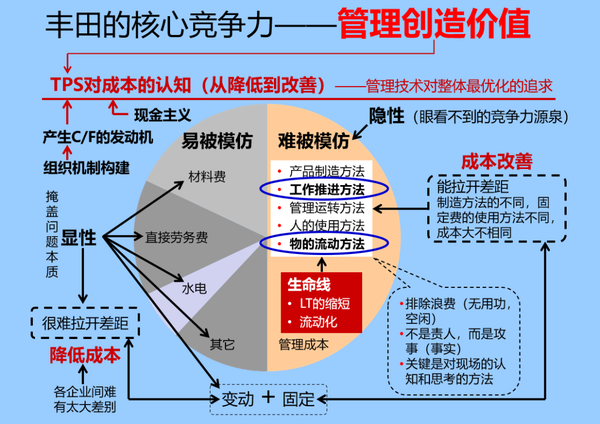
价值流图也是帮助企业完成战略目标的工具。价值流图最佳的用途是把点的改善串联起来,集中力量去应付企业最关键的挑战。在改善过程中,可以用下列问题来做为引导:(1)目前公司的战略目标是什么?(2)产品系列价值流的当前状况如何?(3)价值流未来图如何能帮助企业完成战略目标?
1、VSM是一个呈现问题的工具:
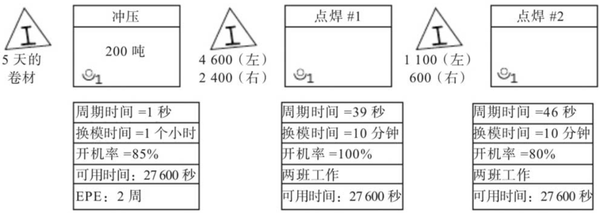
·它可以帮助你看到整个生产流程,而不是单个工序,如装配、焊接等。通过它,你可以看到产品的流动。·它不仅帮助你发现浪费,而且能帮助你找到价值流中浪费的源头。·它提供了一个生产线上通用的语言。
·它帮助你更清楚地了解价值流的改善计划,以便和其他部门沟通。否则,许多操作上的细节将很难确定。·它将精益的技术和概念串联起来,成为一个计划,避免参与者仅选择个人想做的事。
·它是制作实施计划的基础,帮助你设计“门到门”的运作流程,成为实施精益的蓝图。如果不了解其重要性,就会像建房子没有蓝图一样!·它帮助把信息流和物料流联系起来,迄今还没有发现其他的工具能做到这一点。
·价值流图能为你带来的价值远超过其他定量的工具(比如一般描绘生产作业的工厂布置图)。它包括非增值步骤、生产交付期、移动距离、库存等数据。其实,价值流图是一个定性的工具,能帮助你了解如何使产品流动起来。一般情况下,数据可以帮你创造一种紧迫感,或用来作为改善前后的衡量依据,但价值流图能更进一步地帮助你列出如何落实改进的计划。
2.VSM的目的是让问题显现化,通过改善缩短生产周期时间,提升JIT水平
价值流图能帮助你观察现状,并注意其流动的情况,找出一个理想的、逐步改进的生产方式。
- 通过绘制产品的价值流图,了解生产现场的“现状水准以及问题点”,
- 进而让“物料与信息的停滞一目了然”,让问题(物料和信息的堆积、停滞)显现出来。
- 最后通过改善这些问题实现管理水平的提升。
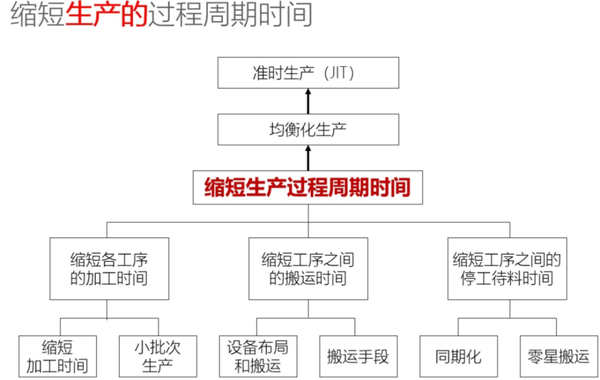
3.VSM的绘制原则:三现主义(现场、现物、现实)
做一个实干、追求生产效益的人,亲自到现场去看,去了解实际情况。无论你是高层管理者还是基层管理者,不要将绘制价值流图的任务分派给下属,然后拼凑起来,这是一种错误的做法。同样,也不要只绘制单个部门的价值流图,而应该绘制整个产品的价值流程图。
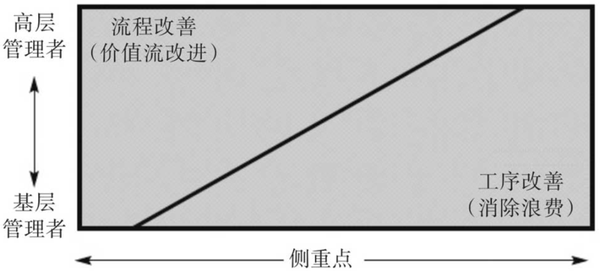
公司既需要整体价值流的改善,又需要工序的改善(在基层消除浪费),两者相辅相成。价值流的改善重点在全面的物料流和信息流,而工序改善的重点则在人员效率和工作流程。
4.价值流图的使用
价值流图是一种沟通的工具、一种商业规划,或者一种管理改善的工具。价值流图按照右图的步骤来进行,其中非常重要的是“未来状态图”。其目标是设计,并实施一条精益的价值流。没有未来状态图,现状图其实没有多大的意义。
- 第一步是收集工作现场的信息和数据,画出现状图,为未来状态图提供所需的数据。请注意现状图和未来图之间的箭头是双向的,这意味着现状和未来状态是相辅相成的。当你绘制现状图时,根据改善计划,未来状态图便自然形成了。
- 当你绘制未来状态图时,可能会发现现状图中一些被忽略的重要信息。
最后一步是用写在纸上的实施计划,描述如何从当前状态转变为未来状 态。
- 在实现未来状态后,应当再绘制一幅新的未来状态图,这就形成了一个持续改善的循环。
价值流图的美妙在于,它不需要繁文缛节,也不需要使用PPT。仅用几张纸绘画出现状图和未来状态图,制订改善计划,并予以实施,就可以改善运营状况。
5. 绘制现状图:通过绘制物料流和信息流,弄清当前的生产运作状态
- 首先沿着整个门到门的价值流,快速地走上一圈,了解整个流程和各个工序,然后回过头来,收集不同工序的数据。
- 应当由发货端开始,朝价值流的上游追溯,而不是从收货端,朝下游推进。这样可以从最接近顾客的工序开始,要注意后端的工序决定上游工序的生产节拍。开始的顺序如下图所示:
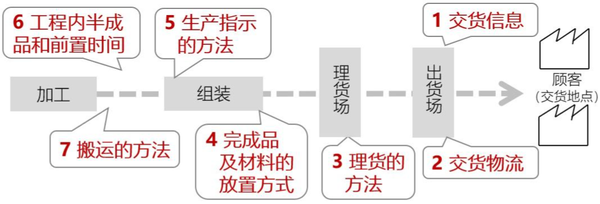
- 带着秒表到现场去测时,不要依赖不是你亲自测量的标准工时或信息。档案文件中的数据往往是在正常的情况下采集的,并不一定反映实际情况。例如本年度第一次换模时间为三分钟;或者是在公司开业的第一周、在没有特殊情况下收集的数据。未来状态图的成败取决于你在现场观察时,对实际状况与数据的掌握(包括机器可靠性、废品率、返工率及换模时间等)。
- 即便有好几个人一同参加价值流图的准备工作,还是应当独立作业,去绘制整个价值流图。这样你才能掌握价值流图的全部,如果每个人负责一部分,那就没有一个人能了解整个价值流。
- 最后,应坚持用铅笔手工绘图。在工作现场进行现状分析时,就开始画草图,然后清理、修正。最好能抵制使用计算机的诱惑。
6.寻找问题点和浪费:消除七大浪费
许多精益改进活动都集中在减少“七种浪费”上,目的是要缩短从原材料到成品之间的生产交付期。其实你需要做的,不仅是消除明显的浪费,更需要消除浪费的源头,然后才能有效地实施精益生产。
浪费最主要的根源是过量生产,也就是上游工序生产的产品,比下一道工序所需要的过多、过早。
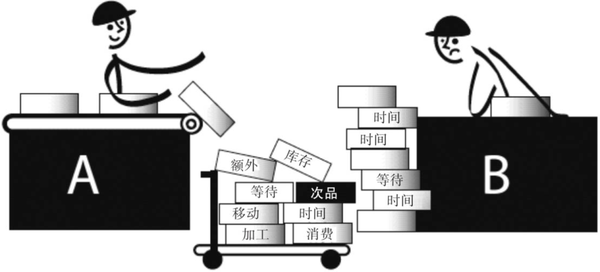
7.精益价值流的特征精益生产最重要的是在顾客或下一道工序需要的时候才生产。将生产流程中所有的工序,从最终顾客到原材料连起来,形成一个没有迂回的流程,达到最短生产交付期、最高质量和最低成本的目的。
如何在车间建立一个在下一道工序需要时,才生产的制度呢?很幸运地,我们可以借鉴丰田公司的经验,参照以下准则:
准则1:按照节拍时间生产节拍时间(takt time)是基于顾客要求的生产节奏。节拍时间用每班可用的工作时间(以秒计),除以顾客的需求量来计算。
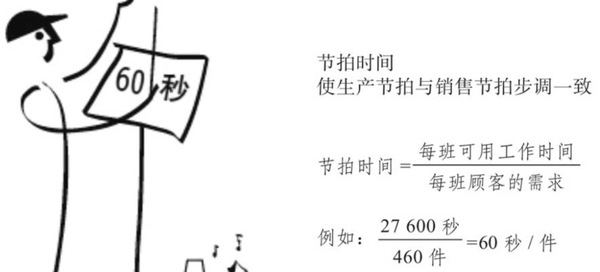
节拍时间是用来协调生产与销售的步调。节拍时间是一个参考数据,让你明白每一道生产工序应该遵守的速率,掌握现况,提出改进的方向。在未来状态图中,节拍时间标注在数据箱中。
按节拍时间生产说起来简单,但实施起来需要付出相当大的努力:·对意外问题做出快速的反应(在节拍时间内);·消除意外故障的原因;·降低下游装配工序的换模时间。
准则2:尽可能创建连续流连续流是指每次生产一件产品,然后从一道工序传到下一道工序,中间没有停顿。连续流是效率最高的一种生产方式,你应当尽可能地采用这种方式。
,时长00:46
准则3:在连续流程无法向上游扩展时,建立一个超市来控制生产
价值流中往往有一些工序不可能实施连续流,必须用批量方式。有几种可能的原因:
- 有些工序的周期时间过长或过短,或需要换模来生产不同的产品(例如冲压或注塑成型);
- 有些工厂距离远,每次运输一小批不现实,例如外协加工的零件;
- 有些配件的生产周期长或生产不稳定,无法与其他工序相连形成一个连续流。
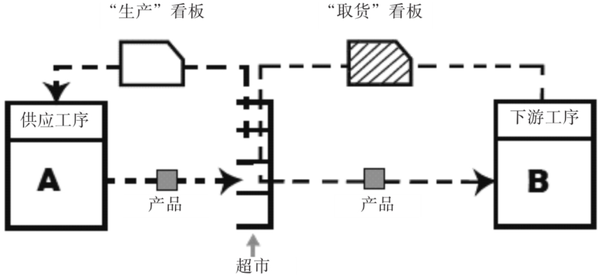
准则4:下达订单到一个点(定拍工序 pacemaker process)
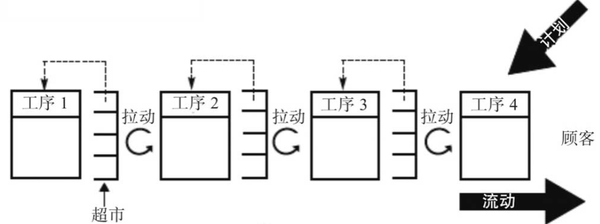
准则5:在定拍工序,均衡地安排生产多种产品
准则6:持续地向定拍工序下达小批量的生产指令通过一个稳定、均衡的生产节拍,可以建立一个可预测的生产流程。其优势是容易发现问题,并促使你迅速解决问题。最容易的入门点,是向定拍工序规律地下达定量的工作(相当于5~60分钟的工作量),并且在同一时间内,取走相等量的产品。我们称这个方法为“定拍取货”。这个稳定、持续的生产量,我们称之为“批量单位”。其数量往往按包装的容量,即每个成品箱能容纳零件的数量来计算。
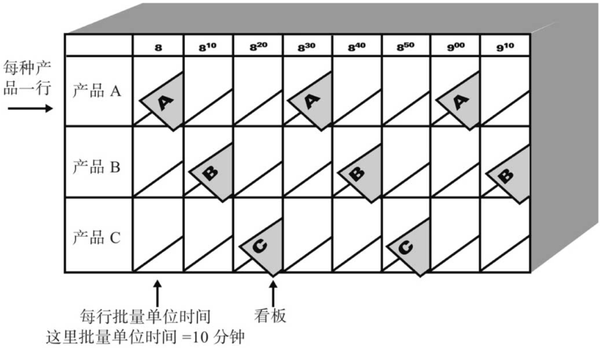
例如,节拍时间=30秒/件,包装容量=20件,批量单位时间=10分钟(30秒/件×20件=10分钟)。换句话说每10分钟:(1)给定拍工序发出一个生产信号。(2)取走一个批量单位的成品。在此例中,批量单位时间是节拍时间乘以定拍工序包装箱的容量。用这个数量作为一个产品系列生产的基本单位。
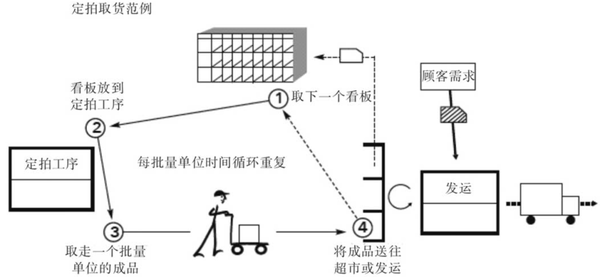
准则7:在定拍工序的上游工序,建立“每天生产每种零件”的能力(希望能持续改善到每班、每小时、每个托盘生产不同的产品)
8. 未来状态图:消除浪费、实现精益的蓝图在开始时,重点应放在短期内无需太大投资就可以启动的改善项目。最终目标是建立一条连续的生产流,让每一道工序都能连续。建立拉动系统与下游工序连接,在顾客需要时,就能生产。
绘制未来状态图最有效的方法是按照顺序回答以下问题。然后根据你的答案,绘制出一幅未来状态图。
- 什么是节拍时间?根据下游最接近顾客工位的可用工作时间来计算节拍时间。
- 建立一个成品仓库,还是直接发运?(这个问题要考虑的因素,包括顾客的购买方式、设备的可靠性以及产品的特征等。如果采用直接交付运输的方法,你需要一个可靠的、交付期短以及能按照订单生产的价值流。否则你必须维持一个相当大的安全库存。幸运的是,按订单生产的交付时间,仅取决于定拍工序以后的作业时间。)
- 哪里可以实施连续流?
- 哪里可以应用超市与拉动系统来控制上游工序的生产?
- 哪一个工位是生产链的定拍工序,可以用来安排生产计划?(请记住:定拍工序以下的工序应该是一个先入先出的移动。)
- 如何在定拍工序里,均衡生产不同的产品?
- 你在定拍工序生产与提取的批量是多少?定拍工序的周期时间要尽可能地接近节拍时间。当节拍时间与周期时间有很大差距时,表示生产线上可能有,没有预期的设备故障问题。如果你用其他方法加快生产速度,使得周期时间低于节拍时间的话,那么消除这个浪费的原动力便消失了!如果你的周期时间比节拍时间短,那么你需要制订计划缩减两者之间的差距。
- 为了实现“流动”的未来状态,必须实施哪些设备与工艺方面的改进?(比如单元生产的模式、缩短换模时间或者提高设备的开[插图]机率等。可以用爆炸点的符号来表示价值流中的改善点。)
精益制造的成功与否有赖于下列几个重要原则:
原则1:加强员工解决问题的能力。
原则2:为高层经理的决策提供有价值的信息。
原则3:原则1应优先于原则2。
一个适用于任何精益工厂的指标:定拍工序每天是否按顾客需求在节拍时间内完成工作?