在制造型企业的生产环节中,时间就是金钱,效率就是竞争力。今天,我们就来聊聊一个能让生产效率突飞猛进的精益生产方法 —— 快速换模(SMED),看它如何帮助企业实现半小时内完成产线切换,开启降本增效的新局面。
传统换模,企业发展的 “绊脚石”
在制造业,生产不同产品时常常需要更换模具和设备。传统换模方式耗时漫长,每次换模,生产线都得长时间停机,这期间设备闲置、人员等待,产生的隐性成本不可估量。
而且,换模过程操作复杂,工人在紧张忙碌中容易出现安装失误,后续还可能引发一系列产品质量问题。频繁的长时间换模,不仅打乱生产计划,还导致订单交付延迟,严重影响企业信誉,这无疑成了企业发展路上的 “绊脚石”。
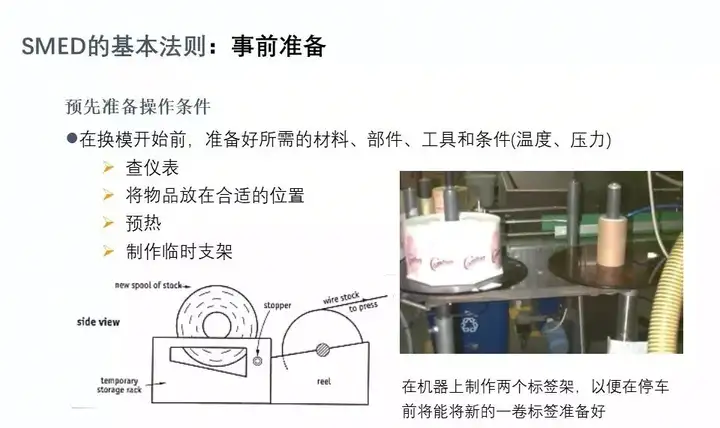
SMED,精益生产的 “魔法棒”
快速换模(SMED)是一种先进的生产改进方法,它的核心目标是把模具更换、设备调试等时间大幅缩短。SMED 通过科学的方法,将换模作业巧妙地分为内部作业和外部作业。
内部作业是设备停机时才能进行的操作,而外部作业则能在设备运行时提前准备。通过将尽可能多的内部作业转化为外部作业,并合理安排各项任务并行开展,SMED 就像拥有魔法一般,让原本动辄数小时的换模时间,缩短至半小时甚至更短。
SMED 实施,步步为营
1. 精准测绘,摸清现状
实施 SMED 的第一步,是要对当前换模流程进行细致入微的观察和记录。精确记录每个换模步骤所需的时间,精准找出耗时较长的环节,深入分析背后的原因,是工具不匹配、操作流程繁琐,还是人员配合不默契?只有摸清 “家底”,才能有的放矢地进行改进。
2. 内外分离,提前准备
清晰区分内部作业和外部作业,是 SMED 的关键环节。将模具预热、工具准备、新模具搬运等工作,提前在设备运行时完成,这些外部作业准备得越充分,设备停机后的换模时间就能压缩得越短。
3. 优化内核,简化操作
对于必须在停机时进行的内部作业,要进行深度优化。比如,采用快速定位、快速夹紧装置替代传统的复杂连接方式,简化模具拆卸和安装步骤,从而显著缩短内部作业时间。
4. 标准引领,规范流程
制定一套详细、标准化的换模操作流程和作业指导书,明确每个岗位、每个步骤的操作要求和时间节点。这既能帮助新员工快速上手,又能确保老员工操作更加规范,提高换模操作的准确性和稳定性。
真实案例,见证 SMED 的力量
某汽车零部件企业在引入 SMED 之前,每次产线切换生产不同型号的零部件,换模时间长达 4 - 5 小时,生产效率低下,生产成本居高不下。实施 SMED 后,企业组建了专业的改善团队,对换模流程进行全面梳理。
他们提前将模具准备、工具校验等工作在设备运行时完成,同时对模具结构进行优化设计,采用了快速定位销和气动锁紧装置。经过持续改进,该企业成功将产线切换时间缩短至 20 分钟以内,生产效率大幅提升,产能提高了 30%,生产成本降低了 25%,在市场竞争中脱颖而出。
拥抱 SMED,开启高效生产新篇
快速换模(SMED)为制造型企业提供了一个提升生产效率、降低成本的绝佳途径。它能让企业在有限的时间内生产出更多优质产品,灵活应对市场的多变需求。如果你的企业还在为换模时间长、生产效率低而苦恼,不妨尝试引入 SMED,相信它会给你带来意想不到的惊喜,助力企业开启高效生产的新篇章。